Customer Satisfaction and Quality
Quality Control Organization
The Pack has established a quality control organization to ensure high product quality, and performs ongoing training and education and other activities related to quality and safety, and considers measures to consider and reflect complaints and irregularities. A quality control supervisory division under the direct supervision of the President has been established as an autonomous section in charge of oversight and supervision quality. This division works with manufacturing quality control sections to improve product quality. In 2023, we established quality control and quality assurance departments within the quality control supervisory division. We are striving to improve quality from a broad perspective through efforts to meet customer needs and improve manufacturing workplaces based on the twin perspectives of quality assurance from the buyer’s point of view and quality control from the manufacturer’s point of view.
Quality control organization chart
A quality control organization has been established at four domestic plants and the headquarters, procurement, and sales groups to unify quality control and improve operations. The quality control supervisory division takes the lead in preventing quality deviations and human error.
A Quality Policy
A Quality Policy: Increasing customer satisfaction through enhanced quality
The Pack strives to improve customer satisfaction by providing safe, reliable, high quality products to customers based on effective product design, development, manufacture, sales, and services, chiefly for its core business of packaging materials. This Quality Policy represents the foundations of our quality improvement activities and the basis of all our initiatives. In addition to meeting the requirements of laws, regulations, and other rules, we make every effort to ensure that the entire organization is aware of the importance of satisfying customer requirements.
Our thinking on quality
The Pack pursues quality to satisfy all our customers. It takes the following three steps to ensure high product quality:
- Thinking about quality first in product development and production
- Striving to improve customer satisfaction and functionality while ensuring stable supply
- Striving to build, maintain, and improve quality control systems.
We also seek to strengthen product quality through ongoing joint efforts with manufacturing subcontractors. We investigate any quality deviations discovered and assess their effects on product quality and the scope of such impact, as well as thoroughly investigating their causes. We identify the underlying causes of such issues and take corrective measures to prevent their recurrence. We are currently building a structure to facilitate urgent reporting and immediate information sharing Companywide in response to complaints or irregularities involving products already delivered.
Traceability
Our plants undertake the following comprehensive management, in accordance with management rules and procedures, based on traceability:
- Using traceable raw materials
- Recording and retaining details of individual manufacturing processes
- Identifying conforming and nonconforming products at each manufacturing process, starting from raw materials acceptance
We also maintain the following systems to swiftly implement initial response, investigations, and countermeasures in the event of a quality issue:
- Use of urgent reporting systems for immediate sharing of information Companywide
- Securing advanced analytical instruments and technologies to identify causes
These management systems are part of our system for minimizing recalls by making it easy to identify the causes of any quality issues discovered in the steps from raw materials acceptance through each manufacturing process, storage, sale, and consumption.
Internal auditing
For internal audits, quality sections undertake careful reviews from an independent perspective to provide opportunities to identify issues and propose improvements on matters that may be easy to overlook in self-inspections. (Internal audits were carried out at 40 facilities in FY2023.) We’ve established a system capable of swift detection and resolution of any quality-related issues among the issues identified, and proposed improvements.
Results of 2023 quality activities
Seeking to provide products with ever higher levels of quality, The Pack implements regular quality improvement activities. We’ve identied quality improvement months all year long and provide quality control training and awareness-raising activities for employees. Other activities aimed at increasing customer satisfaction through higher quality include announcing and thoroughly communicating quality-related information, holding seminars, and holding quality meetings with partner companies.
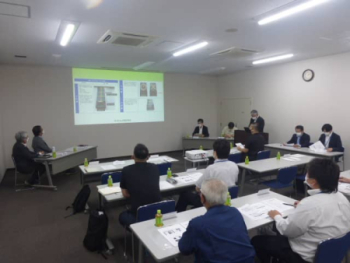
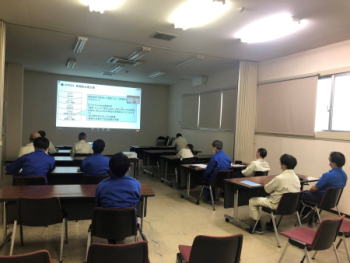
Certifications
We have obtained the following certifications.
All sites in Japan gained ISO 14001 certification for environmental management systems in 2006 and ISO 9001 certification for quality management systems in 2009. We perform periodic internal audits to ensure that the management systems are effectively established.
We have also obtained FSC® CoC certification, which is awarded for paper and paper products incorporating FSC®-certified materials and FSC® controlled wood (FSC® C020517). FSC® CoC certification is awarded by the certification body to certify paper and paper products incorporating raw materials, which were sourced from appropriately managed FSC®-certified forests, and recycled resources.
Additionally, manufacturing lines for paper packaging and containers for food products at the Tokyo Plant and the Osaka Plant have obtained certification under FSSC 22000, an international food safety management system, to assure safe, reliable, high-quality packaging for food products.
Headquarters | ISO14001 ISO9001 FSC® CoC certifications |
---|---|
Tokyo Head Office | ISO14001 ISO9001 FSC® CoC certifications |
Osaka Plant | ISO14001 ISO9001 FSSC22000(specific lines) FSC® CoC certifications |
Tokyo Plant | ISO14001 ISO9001 FSSC22000(specific lines) FSC® CoC certifications |
Nara Plant | ISO14001 ISO9001 FSC® CoC certifications |
Ibaraki Plant | ISO14001 ISO9001 FSC® CoC certifications |
The Pack Quality Control Activities
All sections organize small quality circles to promote operation- and workplace-improvement activities, which improve quality and productivity. Internal awards are presented twice a year to encourage autonomous activities.
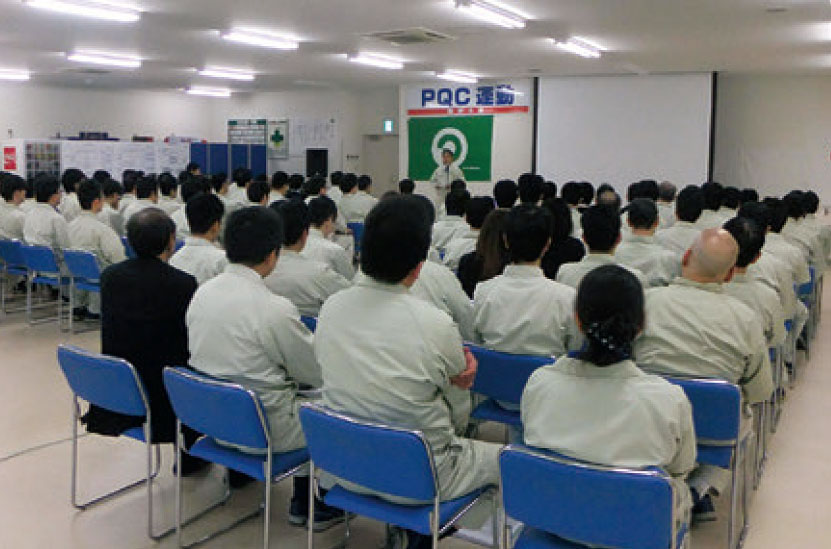
Internal training on quality control
Manufacturing workplaces implement internal training on management of the ‘Four Ms’ (manpower, machinery, materials, and methods) and the ‘Three Hs’ (hajimete [at the start], henko [during changes], and hisasiburi [the first time after a while]).
External quality patrols for partner companies
We conduct checks, guidance, and education through on-site verification and periodic quality patrols.
Co-creation with Customers and Partners
Proposing support for The Pack Forest® Environment Fund
Since 2000, The Pack has contributed a share of some sales of eligible products to The Pack Forest® Environment Fund to support forest conservation activities at nine planting sites across Japan. In 2023, we identified Earning the support of 300 firms for The Pack Forest® Environment Fund as a materiality KPI, and through our packages we are extending the range of contributions to forest conservation activities together with supporting customers. In 2023, 123 companies supported the Fund, and 65 customer personnel participated in the forest conservation activities. We will continue striving to grow the number of supporting firms, as we co-create brand value and foster environmental awareness in society through these activities.
2019年 | 2020年 | 2021年 | 2022年 | 2023年 | |
---|---|---|---|---|---|
Supporting firms(companies)※ | 24 | 44 | 67 | 94 | 123 |
- ※Only companies with actual results are counted.
Logistics modal shift and full-trailer feasibility testing
As measures to address the issue of overtime restrictions in the logistics field beginning in 2024, we carried out feasibility testing of transport using full trailers to improve transport efficiency between plants in eastern and western Japan. With a full trailer, a single driver can transport about twice the cargo of a standard Japanese truck. Results of this testing showed that large-scale improvements in efficiency can be expected. In the future, we will attempt to put full trailers to practical use through investigation of and providing solutions to various issues, such as the workload in preparing to load cargo. We’re also actively pursuing a modal shift using JR rail containers as we strive both to improve transport efficiency and reduce CO2 emissions in logistics.
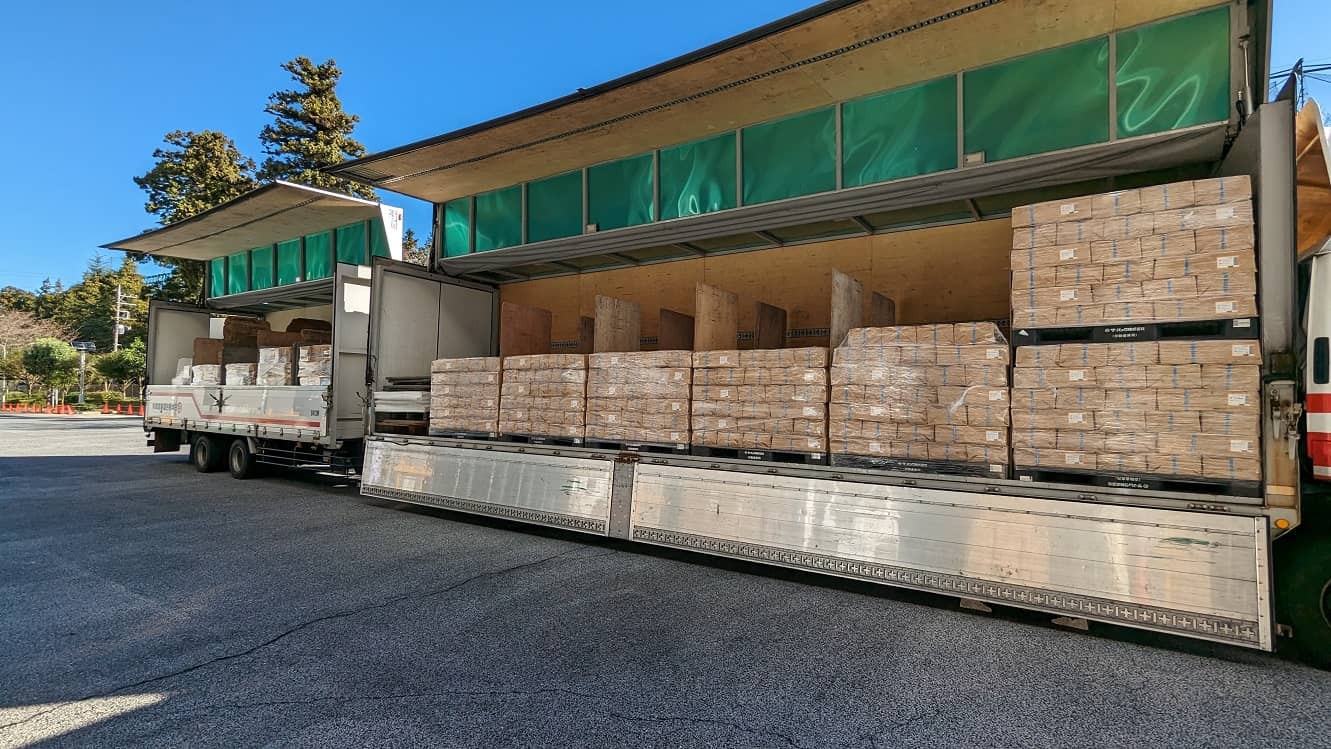
Declaration of partnership building
In order to strengthen coexistence and cooperation throughout the supply chain, the company announced the Declaration of Partnership Building in July 2022. The Declaration will be publicized internally and externally, and efforts will be made to ensure its smooth implementation and enhance the value of the entire supply chain.
Details on the Declaration of Building a Partnership
We will focus on the following points to build new partnerships and promote cooperation, coexistence, and co-prosperity with our supply chain business partners and related value-added companies.
- Coexistence and co-prosperity throughout the supply chain and new collaborations across scale and afiliation: The Company will develop innovative raw materials by utilizing the technologies and know-how of the Company and its suppliers, thus establishing a system of cooperation, coexistence, and co-prosperity between the two parties.
- Adherence to Promotion Standards: We will actively comply with the promotion standards established for the benefit of subcontractors, including the method used to determine subcontractor income, and work to correct any circumstances that may hinder the development of relations between our partners.
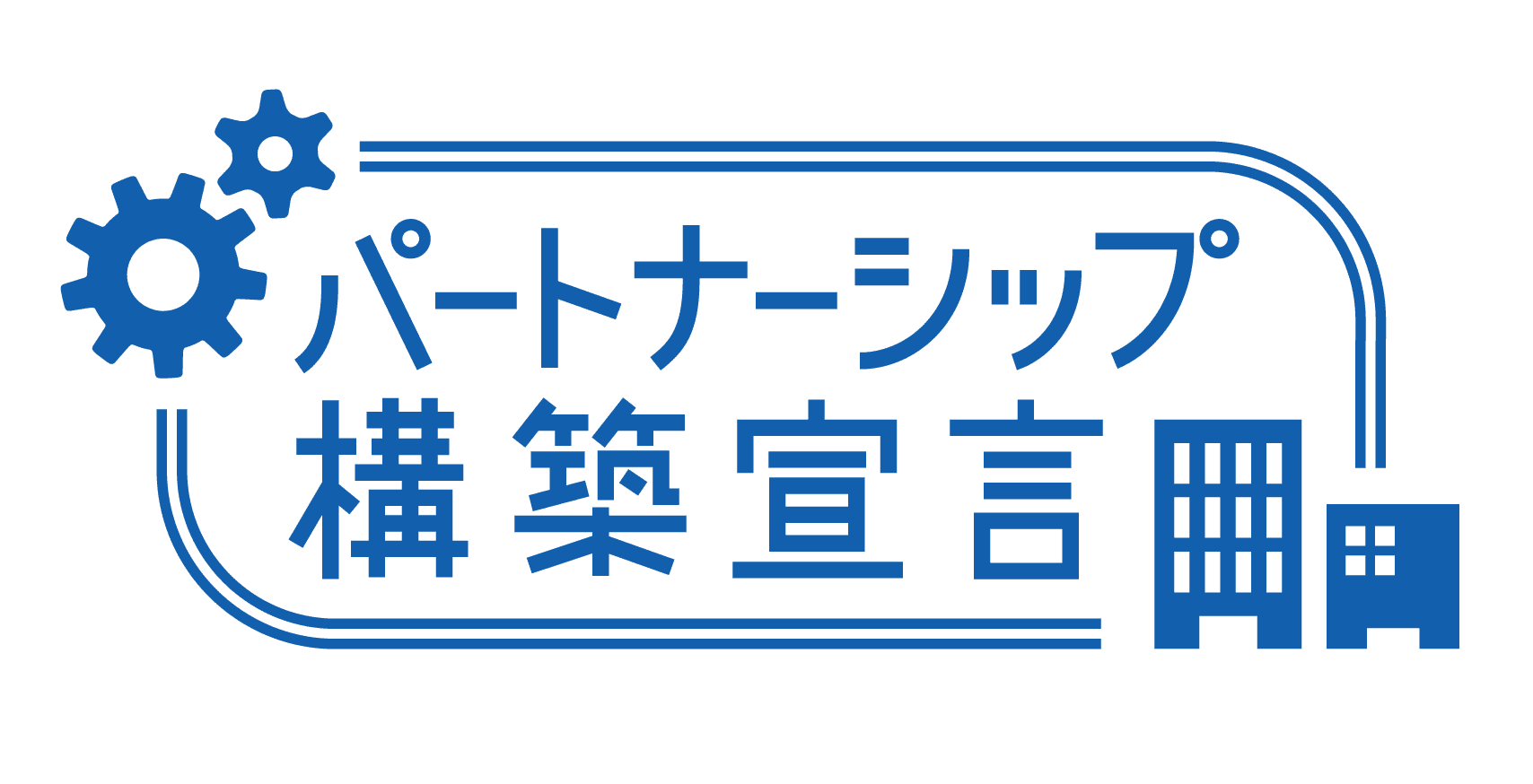
Package Development to Contribute Solutions to Social Issues
ZIGQUICKTM tool developed to support assembly of thin delivery boxes
We developed the ZIGQUICKTM tool to simplify box assembly in response to growing demand for thin delivery boxes. This addresses the need for redelivery and the labor shortfalls at packaging facilities. Made of corrugated cardboard, this tool is lighter and easier to transport than traditional ones made of metal or wood and can be used in safety. We also offer a variable model for which a single unit can handle thin delivery boxes of multiple sizes.
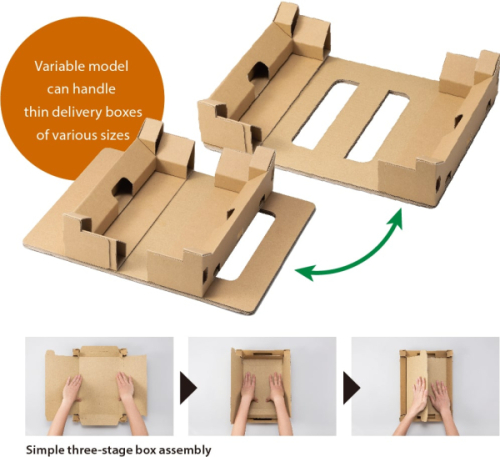
Features
- Remarkably safe and lightweight thanks to corrugated cardboard materials
- A single variable model can be used to assemble boxes of multiple sizes.
- Highly cost effective
Automatic packaging system for paper delivery bags to protect the environment and save labor
In joint efforts with machinery manufacturer Y.A.C. Machinery Co., Ltd., we have developed an automatic packaging system for paper delivery bags in response to the shortage of labor in packaging facilities and to address future environmental needs. By focusing on material structures and machinery design, this system has been designed to enable automatic packaging using paper materials, which previously were difficult to handle in automatic packaging. This system, which allows continuous paper packaging simply by placing the products to be packed on a conveyor belt, controls paper use by automatically detecting product length and packaging the product accordingly. It affixes shipping labels automatically. This packaging system meets the need for both labor savings and environmental protection.